IN DETAIL: Creating Fiber Cement from the Ground Up
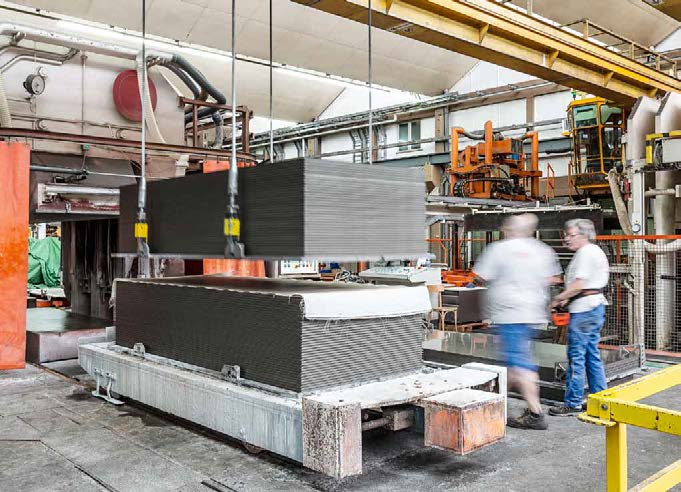
During the 'Back to School' month of September, we're excited to provide some excerpts from a feature in Swisspearl's Magazine - How Are Fiber Cement Panels Created. With over 100+ years of manufacturing experience, Swisspearl® is truly the reference standard in fiber cement manufacturing.
Cladding Corp is pleased to offer Swisspearl® products for exterior rainscreen applications. We firmly believe - not all fiber cement is created equally and this feature will provide insight into the production process of how Swisspearl's signature fiber cement is created.
Download the full article excerpt by Michael Hanak here.
Product Manufacturing History
Several factories in Switzerland, Austria, Germany, and Slovenia manufacture Swisspearl fiber cement products. The plant in Niederurnen, has been located in the midst of the Swiss Alps for more than 100 years. History into the creation of fiber cement dates back to 1901, when Ludwig Hatschek patented his “Procedure for the manufacture of artificial stone plates from fibrous materials and hydraulic binding agents,” and registered “Eternit” as a brand name. With this, he specified the mixture of cement and fibers as well as the production process using a rotating cylindrical sieve. The inventor’s goal was to produce a light, durable building panel. The products made by this process are weather-, corrosion-, frost-, and UV resistant, rot- and fireproof, relatively light, and mechanically processable. While the production process has basically remained the same, it is continually optimized; today, mostly for ecological reasons. More than 90 percent of the raw materials, primarily the cement, are delivered by train from the closest factory of Holcim (Switzerland) AG in Untervaz, and roughly one-third of the products are carried away by train. The engineers are proud of the closed water circuit with two wastewater treatment plants. Water and fresh “green” fiber cement waste segments are directly returned back into the production process. The hard-aggregate waste can be recycled in the cement factory and remixed with the cement. Natural gas generates the production heat required for the paint and panel drying ovens.
Since 2018, the factory has been linked up with the district heating network; surplus heat from the nearby refuse incinerator is used to heat its production halls and warehouses. Special customer wishes—which almost exclusively concern the form, color, and format of the panels—are also taken into consideration; the team gladly complies after successful feasibility studies. However, long, elaborate tests forego any changes in the composition of the material as new materials might limit the panel’s function and must be newly licensed for export, which is tied with high costs and great effort. The production specialists rule out any compromises. Product quality is a top priority.
Starting Material
1. What fibers are used to produce fiber cement panels?
The main raw materials are cement, synthetic fibers, pulp, and water; color pigments are added to that. Pulp is the term used for the fibrous mass that arises during the chemical decomposition of plant fibers, which is comprised primarily of cellulose. After the danger of inhaling asbestos became known in the 1970s a broad research program was introduced in Niederurnen to find a replacement. The first trials and initial new production took place between 1981 and 1989. Since May 1, 1990, all products for building construction from the factories in Niederurnen and Payerne have been free of asbestos. The synthetic fibers (PVA), which provide reinforcement, are from Japan. The pulp is from various countries, including Austria.
Mixture
2. How and in what order are the starting materials processed and mixed?
First, bales of pulp are dissolved in water and milled to the desired fineness. This slurry is added to the pulp and synthetic fibers. The mixture is prepared in large vats in such a way that hydrogen bridges form during the chemical process, which holds the ingredients together. Finally, the cement is added to the intensive mixer. Now the setting process begins.
Panel Machines
3. How does the so-called panel machine work?
The panel machine, which was supplied by the Swiss company Bell, is the heart of the production facility. Three cylindrical sieves rotate in the cement-fiber-water slurry. The rotation leads to the formation of a ca. 0.9-millimeter-thin layer, which is wound around the format roll as often as is required until the necessary thickness has been achieved. This process takes between 20 and 100 seconds, depending on the panel’s dimension and format. The diameter of the format roll determines the length of the panel, which achieves its raw format by means of an appropriate cutting blade. To produce a different format, these units have to be changed. Only experienced Swisspearl employees work on the panel machines. They control the measuring devices, but also use their eyes and hands.
Pressing and Drying Facility
4. How are the raw panels dried?
First, the piled-up panels are pressed under a pressure of up to 10,000 tons with steel sheets as intermediary layers, in order to release the extra water. The water content of the panels thereby is reduced from 28 to 15 percent, and the panel density is increased. The cement continues to harden by chemical reaction with water. Heat is released during this process. The material has enough time to hydrate and solidify. After three weeks of setting, the water content remains only at 7 to 8 percent, and the panels are ready for further processing. In the first step, the panels are dried in an oven. In contrast to autoclaved fiber cement, which is steam hardened in autoclaves, air-dried fiber cement is less porous and can be processed more easily.
Coating Plant
5. What colors can be applied?
A standard assortment of color shades is available, which covers most customer demands. On request, however, almost any color can be applied to the panels. The standard range includes glazes and opaque colors as well as the Carat family for which the colors are applied onto panels with molded-in color. The paints are poured or sprayed onto the panels. Reflex coating offers also an iridescent series of hues with a hammer blow effect. With the Avera range, introduced three years ago, no additional color pigments are used in the coating and thus Avera shows the mass-colored fiber cement in its most natural form.
Cut and Finish
6. What formats and surface finishes are possible?
The maximum standard format that we produce is 3,070 × 1,250 millimeters. Swisspearl is currently adapting to market demand and is increasing the standard panel width by 20 millimeters. There are five standard formats for large-format panels, from which all formats can then be cut. Swisspearl is constantly in search of special surface finishes.
Download the full Swisspearl Magazine - Issue 27 here.